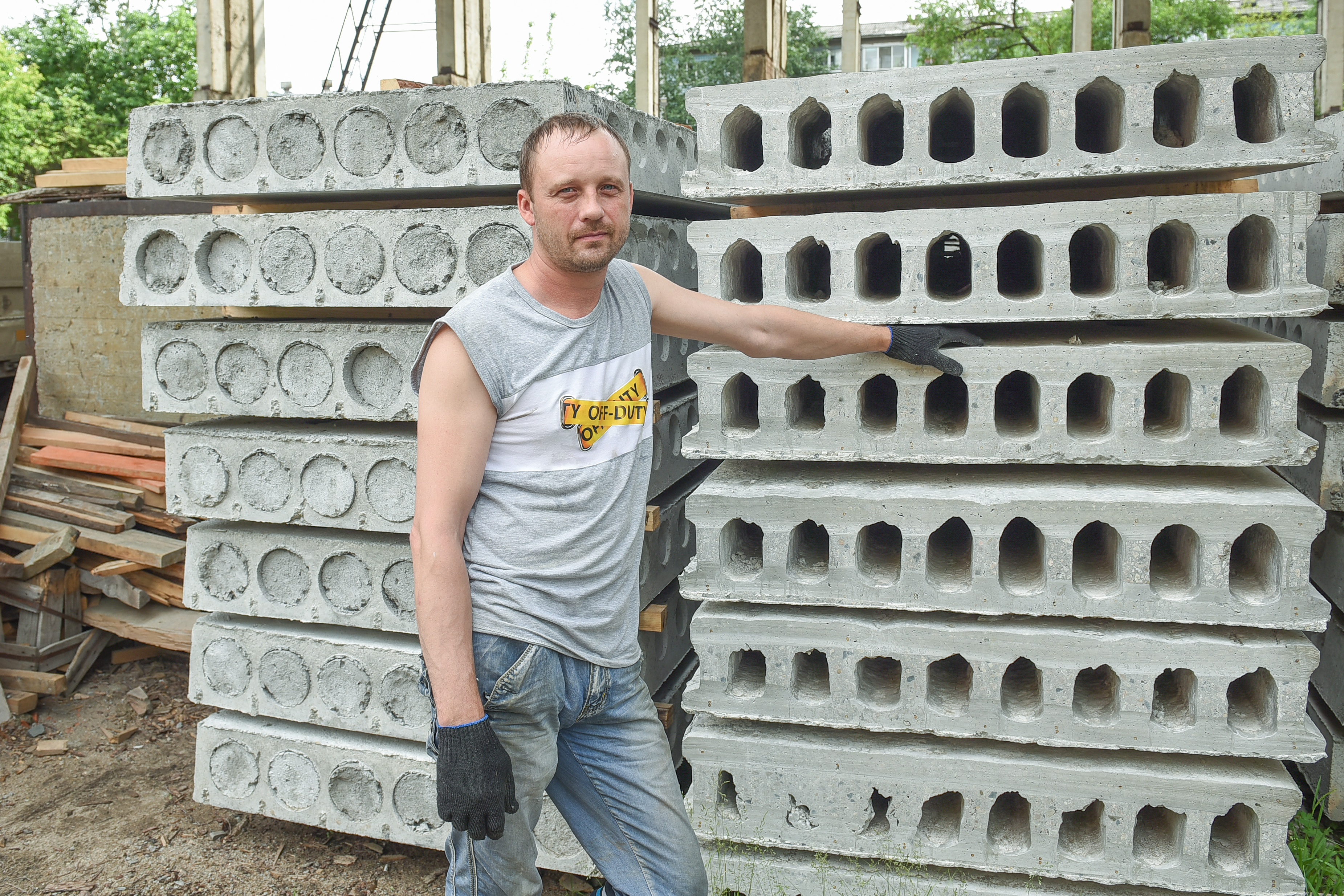
Техника позволяет экономить силы
Основная достопримечательность формовочного цеха — огромный агрегат. В нем замешивают бетон, который выходит после такой процедуры под высоким давлением, напоминая выдавливаемый из мясорубки фарш. Специальная машина заливает им напольные дорожки. Всего их в цехе пять, каждая имеет длину 90 метров.
— Это безопалубочное производство плит и свай по испанской технологии, —рассказывает Андрей Журавлев. — На полу установлен железный поддон, в нем — проволока под определенным натяжением. После заливки бетоном дорожки равняются с помощью специальной машины и пропариваются в течение суток. После еще одна машина пилит их на части по нужным размерам. Готовый продукт вынимают и складируют с помощью крана.
Изготовленные безопалубочным способом материалы имеют значительный запас прочности, что очень актуально в нашем сейсмически активном регионе, поэтому в строительной отрасли Приамурья они пользуются повышенным спросом.
— Когда я пришел работать на завод, производство плит здесь шло только с применением опалубки, — вспоминает Андрей Викторович. — То есть для начала мне с моей бригадой повезло работать по испанской технологии. Когда начинали осваивать новый метод производства, сразу поняли, что это — мощь и сила. Помню, как пошла первая такая бетонная дорожка. Был полный восторг, потому что не понадобилось работать ни лопатой, ни кувалдой, как мы привыкли. Процесс автоматизирован — все на кнопочках, ручного труда намного меньше, поэтому работать легче. Техника позволяет человеку экономить силы. Так что между двумя вариантами производства разница ощутимая.
Отличная команда точка притяжения
30 бетонных дорожек в общей сложности заливает по испанской технологии бригада. Из них получаются 1 500 коротких плит по два метра либо 300 длинны
В бригаде Андрея Журавлева трудятся еще три формовщика и крановщик. О своих подчиненных бригадир говорит: «Отличная команда! Командовать, по сути, и не надо — все знают свою работу и ответственно ее выполняют.» Он признается, что именно дружный коллектив на заводе стал для него той самой точкой притяжения, которая много лет прочно держит его на рабочем месте. «Люди здесь хорошие, — отмечает собеседник, — очень комфортная атмосфера, в которой приятно находиться и общаться. Даже в сложные периоды, когда появлялась необходимость работать в три смены, в коллективе не бьmо каких-то ситуаций, чтобы сотрудники нервничали, ругались. Все выполняли свои обязанности дружно и слаженно. Да, работа формовщика физически сложная, но к такой нагрузке быстро привыкаешь. Так же, как ик шуму-традиционному спутнику заводского производственного процесса. С годами просто перестаешь обращать на него внимание — вообще не мешает. А запах бетона уже давно стал родным».
«Я не халтурю»: как работать без изъянов
Даже в том, что в цехе от пропариваемого бетона регулярно повышается температура, Андрей Журавлев находит плюс. «Зимой у нас очень тепло — можно ходить в футболках», — улыбается бригадир. За месяц его бригада заливает по испанской технологии в общей сложности 30 дорожек, из которых получаются 1 500 коротких плит по два метра либо 300 длинных — каждая по девять метров.
— Я свою работу не просто делаю, лишь бы день отстоять и как получится, мне нужно обязательно получить моральное удовлетворение от процесса и результата, — замечает Андрей Викторович. — Не люблю, когда что-то неправильно, поэтому не халтурю. Надо, чтобы все было выполнено четко, правильно и без изъянов. Приятно, что на заводе есть стабильность. Даже когда я пришел сюда работать в постперестроечные годы, производство еще только налаживалось после экономически сложного периода, но зарплату нам уж:е тогда платили без задержек. А сейчас тем более, всегда все в срок. Это тоже хороший стимул работать. В преддверии юбилея желаю предприятию процветания и долголетия, рабочему коллективу и руководству — здоровья и сил. Пусть спрос на нашу продукцию растет, а объемы производства увеличиваются.
Из повара-кондитера — в формовщики
В первый раз на завод ЖБИ-12 Андрея Журавлева еще мальчишкой привел отец, который в то время был бригадиром в арматурном цехе. Деловито он водил сына по огромной территории и объяснял, чем занимаются сотрудники. Андрей Викторович вспоминает: наблюдал за их работой с большим интересом, а особенно нравились ему огромные агрегаты, издающие громкий шум.
Обстоятельства сложились так, что после окончания школы выпускник поступил в профессиональное училище, где выучился на повара-кондитера, а потом ушел в армию.
Бетон выходит из огромного aгpeгaтa под высоким давлением, напоминая выдавливаемый из мясорубки фарш.
— Отслужил как положено и, вернувшись домой в Благовещенск, сразу поехал к отцу на завод, — рассказывает собеседник. — Тогда мне и предложили поработать формовщиком. Я решил попробовать и принес трудовую книжку.
Было это в 2005 году. С тех пор прошло уже 17 лет, а я все здесь, и уходить куда-то мысли не возникает.
Кстати, младший брат Андрея Журавлева, который вместе с ним в детстве тоже бывал у папы на экскурсиях, работает в одном из цехов завода. Оба сына пошли по стопам отца, сформировалась трудовая династия. Отдав производству много лет, глава семьи вышел на заслуженный отдых, а сыновья остаются на трудовой вахте. «Сложнее всего мне было работать на заводе в первые годы, — признается Андрей Викторович, — тогда я молодой был, после армии хотелось погулять, где-то не высыпался. (Смеется.). А сейчас труд в удовольствие, тем более с испанской технологией.
На правах рекламы
Возрастная категория материалов: 18+
Добавить комментарий
Комментарии